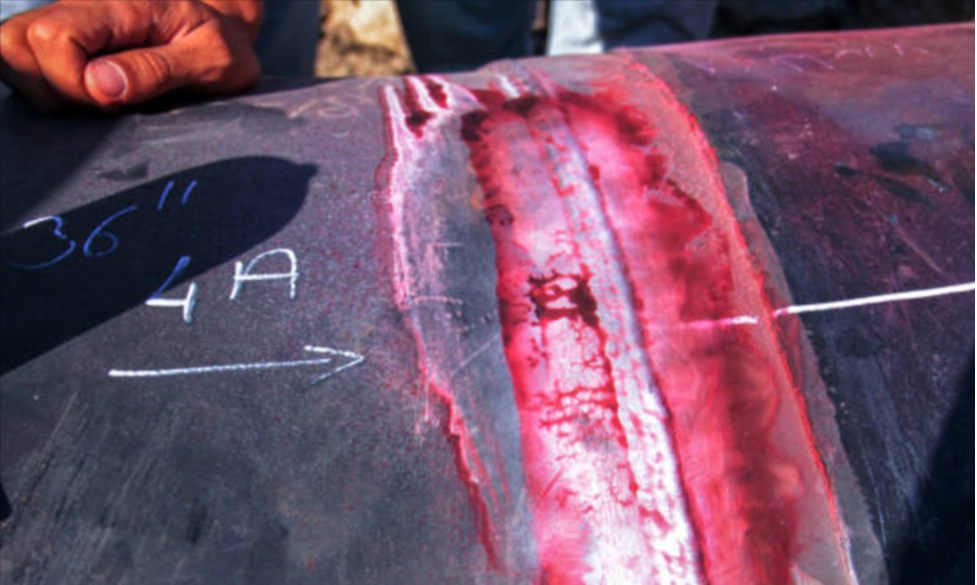
In the field of metallurgy and failure analysis, there are two major types of tests performed on failed parts. The first method involves removing the component from service and sectioning it. The second method allows the failure analyst to investigate the physical properties of the metal without removing the component from service. In general, the former is used to detect and prevent catastrophic failure before it occurs. However, it may be necessary to perform a failure-analysis test on a component that is still in service.
The process of failure analysis starts with the positive identification of the material.
- The first step in this process is to determine the type of alloy that is used in the component. This will allow the engineer to guess the material’s mechanical properties based on the chemical composition and compatibility of the component. Secondly, he can define the scope of his investigation by studying inclusions and foreign deposits in the part. Furthermore, failure analysis can help determine the time-course of the fracture propagation.
- The second step is the failure analysis itself. The failure analysis procedure involves testing the material before and after the incident. A number of different tests are performed on the sample to identify where the fault occurred. A metallurgist’s work involves microscopic examination as well as mechanical testing. The material’s toughness, stiffness, and strength are tested to determine if the defects are the result of a failure. In addition to this, the metallurgist must also look for inclusions that can affect the structure.
- The next step in metallurgy and failure analysis is to analyze the material. To accurately assess a material’s characteristics, he must examine its composition. In addition to assessing the material’s composition, he must also determine the type of alloy used. The type of alloy allows the engineer to guess the mechanical properties of the material and define its scope. The next step is to study the inclusions and foreign deposits. Inclusions are important because they can give a good idea of how the fracture propagated.
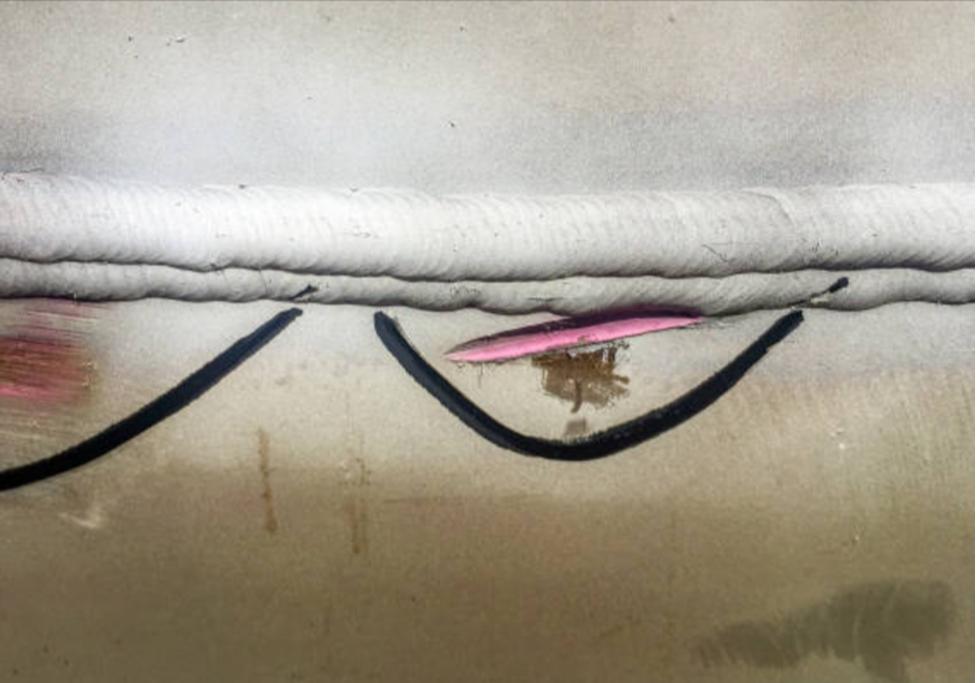
- For example, a metallurgist can perform a failure analysis using a SEM. The results from this process can reveal the root cause of a failure and provide information for preventive measures. In addition, a metallurgist can use the results of the study to create an effective solution to a problem, thus ensuring quality and safety. And if a part is broken, the materials should be replaced in a timely manner.
- The analysis process helps engineers to understand the failure modes of a material and to isolate the cause of the failure. A thorough understanding of the various factors involved in the fracture will help identify the root cause of a failure. In some cases, a metallurgist will find that a fracture is caused by a defect in the material. In other cases, a metallurgist can identify the origin of the failure by examining the cracking surface.
- Metallurgists may perform a failure analysis to determine how a material will fail. For example, they may analyze the material’s composition to understand the origin of a fracture. By analyzing the failure mechanism, engineers can understand how to minimize the effect of the failure on a material. They can also study the manufacturing conditions of the metal. In addition, the metallurgist can perform chemical and mechanical tests.
- The metallurgical part of failure analysis involves investigating the cause of a failure and identifying the factors that contributed to the failure. The metallurgist’s role is to determine whether a product’s failure is caused by a defect in the material’s composition. It also examines the materials’ failure mechanisms to assess the reasons for their damage and how they might be repaired. Further, this analysis will allow them to make the right decisions for the replacement of the product.
The Bottom Line
The metallurgist’s role in metal failures is crucial to the safety of our society. Considering the varying types of metal failures in different industries, the role of Origin and Cause – metallurgical and materials engineering is critical to the overall success of these industries. Therefore, the metallurgist’s findings in these areas are vital to the quality of products. They can determine whether a product is safe or unsafe by determining the cause of the failure.