In industrial plants, where harsh toxins, heavy machinery, and constant foot traffic are the norm, the flooring system plays a critical role in maintaining safety, durability, and efficiency. Chemical exposure can damage standard materials, leading to costly repairs, operational downtime, and safety hazards. This is where chemical-resistant systems come in.
Designed to withstand harsh substances and demanding conditions, these specialized surfaces offer long-term benefits for industrial environments. In this blog, we’ll explore the top reasons to install chemical-resistant floors in plants and why they are a smart investment for industrial operations.
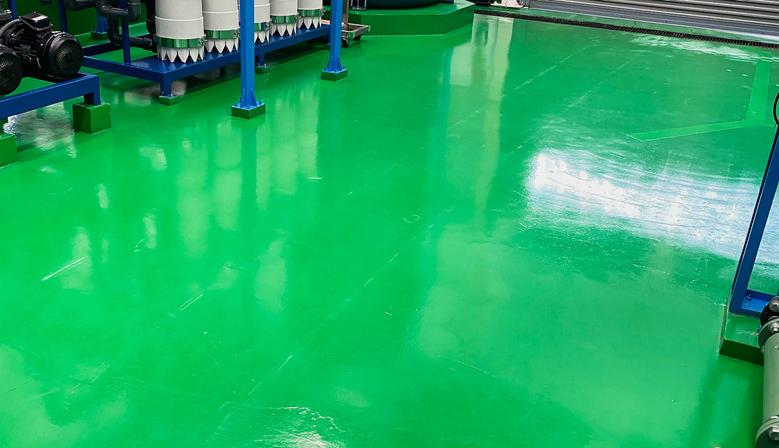
Protection Against Corrosion and Chemical Damage
One of the primary reasons industrial plants install commercial epoxy floors is to protect against corrosive substances. Facilities such as chemical plants, pharmaceutical labs, and food processing plants often handle aggressive liquids, including acids, solvents, and cleaning agents. Traditional materials like standard concrete or vinyl can degrade quickly under toxic exposure, leading to cracks, erosion, and structural damage.
Chemical-resistant systems, such as epoxy or polyurethane coatings, create a protective barrier that prevents harmful substances from penetrating the surface. This extends the lifespan and reduces the frequency of costly repairs or replacements.
Enhanced Workplace Safety
In industrial settings, safety is always a top priority. Toxic spills and leaks can create slippery surfaces, increasing the risk of accidents, injuries, and potential liability claims. Chemical-resistant floors are often designed in a collaborative process with anti-slip properties, ensuring that even in the event of spills, workers have better traction and stability.
Additionally, these systems resist toxic absorption, which minimizes hazardous fumes or residues that could pose health risks. With a chemical-resistant surface, you create a safer environment for employees, reducing hazards.
Compliance with Industry Regulations
Many industries are subject to strict safety, health, and environmental regulations. Regulatory bodies such as OSHA (Occupational Safety and Health Administration) and EPA (Environmental Protection Agency) enforce guidelines on how industrial plants must handle and manage toxin exposure, spills, and waste.
Installing chemical-resistant flooring ensures compliance with these regulations by minimizing the risks associated with spills and contamination. Meeting these standards not only keeps employees safe but also protects businesses from costly fines, legal actions, and operational shutdowns.
Cost-Effective Long-Term Investment
While the upfront cost of chemical-resistant options may seem higher than traditional systems, it’s a cost-effective long-term investment. Standard floors exposed to harsh toxins require frequent repairs, resurfacing, and even full replacements. These recurring costs add up over time, not to mention the financial burden of operational downtime during repairs.
Chemical-resistant surfaces are designed to withstand repeated exposure without deteriorating, saving money on maintenance and reducing costly interruptions to production. In the long run, their durability and resilience make them an economically smart choice.
Easy Maintenance and Cleaning
Industrial plants require frequent cleaning and sanitation to maintain hygiene and operational standards. Chemical-resistant floors are typically non-porous and seamless, preventing toxins, oils, or other contaminants from seeping into cracks or joints.
Their smooth surfaces make them easy to clean and sanitize using standard industrial cleaning products. This minimizes labor costs, reduces cleaning time, and ensures that spills or leaks don’t become long-term problems.
Increased Durability in Harsh Environments
Industrial plants often experience heavy foot traffic, exposure to high temperatures, and the constant movement of heavy equipment or machinery. Surfaces that crack, chip, or erode under these conditions can cause costly disruptions and safety hazards.
Chemical-resistant systems are engineered for maximum durability. They can endure thermal stress, mechanical impact, and repeated exposure to corrosive substances without losing their structural integrity. This level of durability ensures a reliable, long-lasting solution that can keep up with the demands of industrial operations.
Customized Solutions for Specific Needs
Every industrial plant has unique operational needs, and chemical-resistant surfaces can be tailored to meet these specific requirements. Whether it’s additional anti-slip properties, resistance to thermal shock, or specialized coatings for high-traffic areas, these floors offer customizable solutions to match the demands of each facility.
Specialized coatings can also include visual markers, such as color-coded zones for safety areas, spill containment barriers, or walkways, enhancing both safety and operational efficiency.
The Bottom Line: A Smarter Choice for Industrial Plants
Chemical-resistant floors are more than just a protective layer—they’re a crucial component of a safe, efficient, and cost-effective industrial workspace. By investing in these specialized systems, industrial plants can prevent costly damage, improve workplace safety, comply with industry regulations, and enhance overall productivity.
Whether you’re building a new facility or upgrading an existing one, installing tough surfaces is a strategic investment that pays off in durability, safety, and peace of mind. Don’t wait until chemical damage becomes a costly problem—proactively protect your workspace with flooring designed to withstand the toughest conditions.